High Precision Plastic Injection Molding: Revolutionizing Manufacturing
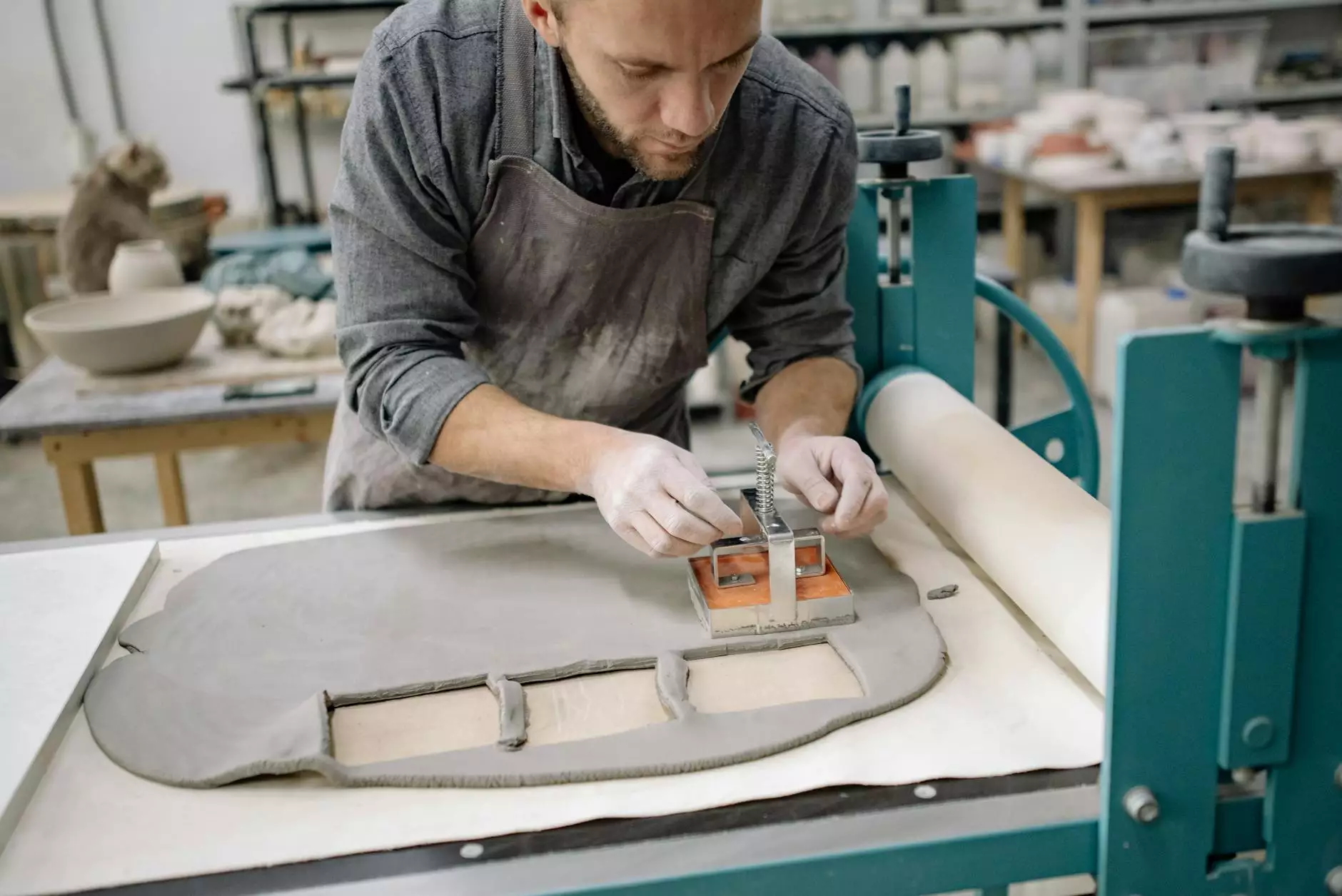
In today's rapidly advancing world, the demand for high precision plastic injection molding has grown exponentially. This manufacturing process not only allows for the production of intricate designs but also ensures a level of precision that is unmatched by traditional methods. In this comprehensive article, we will delve deep into the nuances of this technology, exploring its applications, benefits, challenges, and future prospects.
Understanding High Precision Plastic Injection Molding
At its core, high precision plastic injection molding is a manufacturing process that involves injecting molten plastic into a mold to create various products. This technique has gained traction due to its ability to produce complex shapes and high tolerance parts accurately and efficiently.
How It Works
The process begins with the melting of plastic pellets in a heated barrel. Once melted, the plastic is injected into a mold at high pressure. After cooling, the mold is opened, and the finished product is ejected. This method is particularly advantageous due to its:
- Speed: The production cycle can be incredibly quick, often taking just seconds or minutes for each item.
- Consistency: Each product is nearly identical, providing uniformity essential in many applications.
- Versatility: Suitable for various types of plastics, including thermoplastics and thermosetting plastics.
Applications of High Precision Plastic Injection Molding
The versatility of high precision plastic injection molding makes it applicable across multiple industries. Here are some of the critical domains where this technology is widely used:
1. Automotive Industry
Automotive parts require robust design and durability. High precision plastic injection molding enables manufacturers to produce components such as bumpers, dashboard panels, and interior fittings with exceptional accuracy. This reduces weight and enhances fuel efficiency.
2. Electronics
In the electronics sector, the demand for intricate and compact designs is paramount. High precision molding allows for the creation of casings, connectors, and various electronic components with tight specifications, ensuring functionality and safety.
3. Medical Devices
In healthcare, the importance of precision cannot be overstated. High precision plastic injection molding is used to manufacture medical devices, syringes, and other critical components that must adhere to rigorous standards and tolerances.
4. Consumer Products
From kitchen appliances to toys, consumer products benefit immensely from this technology. The ability to produce complex designs quickly makes it ideal for creating packaging, bottles, and intricate assembly parts.
Advantages of High Precision Plastic Injection Molding
Choosing high precision plastic injection molding over other manufacturing processes presents numerous advantages, including:
1. Cost-Effectiveness
Although the initial setup cost can be high, the long-term savings are significant. The efficiency of the process reduces material waste and energy consumption, lowering overall production costs.
2. Quality Control
Thanks to advanced technology and sophisticated machinery, manufacturers can achieve high levels of quality control, ensuring that each product meets specific standards. Automated processes help eliminate human errors and improve product reliability.
3. Scalability
This molding technique allows companies to scale their production rapidly. Whether producing small batches for prototypes or large volumes for mass production, high precision plastic injection molding accommodates both needs efficiently.
Challenges in High Precision Plastic Injection Molding
While the advantages are compelling, it is essential to understand the challenges that can arise within the high precision plastic injection molding process:
1. Initial Costs
The upfront investment in machinery, molds, and technology can be significantly high. This may deter smaller companies from adopting this sophisticated process.
2. Design Limitations
Although highly versatile, some designs may still pose challenges in terms of mold creation, leading to potential compromises in the design of the final product.
3. Material Limitations
Not all plastic materials are suitable for every application. Understanding the materials’ properties and their compatibility with injection molding machinery is critical for success.
The Future of High Precision Plastic Injection Molding
The future of high precision plastic injection molding looks promising as technology continues to evolve. Here are some potential developments to watch:
1. Advancements in Materials
Innovations in bioplastics and composite materials will enable more sustainable manufacturing practices, allowing companies to produce eco-friendly products without sacrificing performance.
2. Automation and Industry 4.0
The integration of smart technology and automation will enhance efficiency and precision. Predictive maintenance and real-time quality control will help manufacturers optimize their production processes further.
3. Customization through 3D Printing
3D printing technology is beginning to intersect with high precision plastic injection molding. The ability to create complex molds using 3D printing can reduce lead times and enhance customization.
Conclusion
High precision plastic injection molding is more than just a manufacturing process; it is a catalyst for innovation across various industries. With its ability to deliver precise, efficient, and cost-effective solutions, it is no wonder that companies are increasingly turning to this technology. As trends in design, materials, and smart manufacturing evolve, the future of high precision plastic injection molding is undoubtedly bright.
For organizations seeking a reliable partner in navigating the complexities of high precision plastic injection molding, Deep Mould has positioned itself as a leader in the industry, combining decades of expertise with cutting-edge technology. Visit DeepMould.net to learn more about how high precision plastic injection molding can transform your business today.