Understanding GRP Composite Housings: Benefits, Applications, and Future Trends
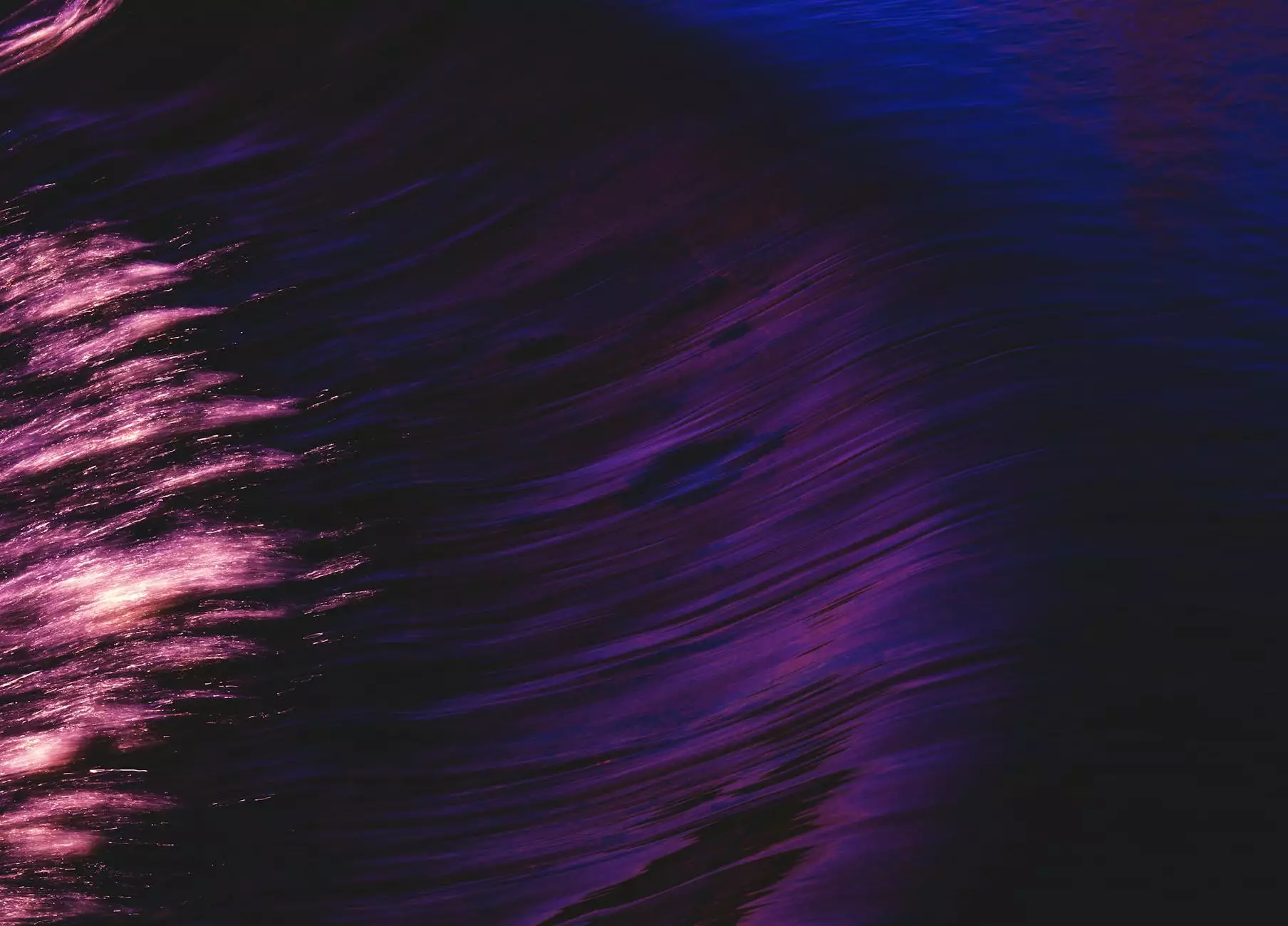
GRP composite housings represent a significant advancement in material technology, combining the strength of glass fibers with the versatility of plastics. As industries strive to improve efficiency, reduce costs, and enhance product longevity, GRP composite materials are becoming indispensable in modern manufacturing and construction. In this article, we will delve into the multifaceted world of GRP composite housings, examining their benefits, applications, and future trends.
What are GRP Composite Housings?
Glass-Reinforced Plastic (GRP), also known as fiberglass, is a composite material made from a polymer matrix reinforced with glass fibers. This unique combination results in a material that is not only lightweight but also possesses remarkable mechanical strength and corrosion resistance.
The Composition of GRP
The primary components of GRP include:
- Fiberglass: Provides structural integrity and strength.
- Resin: Binds the glass fibers together and offers waterproofing properties.
- Additives: Enhancements for UV resistance, fire retardation, and improved durability.
Advantages of GRP Composite Housings
The use of GRP composite housings presents numerous advantages over traditional materials such as metal or wood:
1. Lightweight Yet Strong
One of the most compelling benefits of GRP composite housings is their lightweight nature, which does not compromise their strength. This characteristic leads to reduced transportation costs and easier handling during installation.
2. Excellent Corrosion Resistance
GRP materials are inherently resistant to a wide range of corrosive substances, making them ideal for applications in the chemical, marine, and wastewater industries. Unlike metals, GRP does not rust or corrode, ensuring a longer lifespan.
3. Cost-Effectiveness
While the initial investment in GRP composites may be higher than some alternatives, their durability and low maintenance requirements provide significant long-term savings. Businesses can expect reduced replacement costs and improved operational efficiency.
4. Versatility and Customizability
GRP composite housings can be molded into virtually any shape and size, allowing for customized solutions that meet the specific needs of various industries. This flexibility enables designers and engineers to innovate without limitations.
5. Thermal and Electrical Insulation
GRP materials also offer excellent thermal and electrical insulation, making them suitable for a wide array of applications, from electrical enclosures to thermal storage solutions.
Applications of GRP Composite Housings
The versatility of GRP composite housings makes them suitable for numerous applications across diverse industries:
1. Electrical and Telecommunication Enclosures
GRP is widely used to manufacture electrical enclosures, as it protects sensitive components from environmental factors while providing excellent insulation. Its lightweight nature permits easy installation, especially in remote or difficult-to-access locations.
2. Automotive Industry
In automotive manufacturing, GRP composite housings are increasingly utilized for body panels and structural elements due to their strength-to-weight ratio, contributing to better fuel efficiency and performance.
3. Marine Applications
Given its exceptional resistance to saltwater, GRP composite housings are perfect for marine applications, such as boat hulls and harbor infrastructure, ensuring longevity and durability in harsh environments.
4. Wastewater Management
In the wastewater sector, GRP is used for tank linings, pipes, and various other components due to its ability to withstand corrosive effluents, extending the lifespan of municipal systems.
5. Construction Sector
The construction industry benefits from GRP composite housings in the form of skylights, roofing systems, and structural panels, thanks to their durability and insulation properties.
How GRP Composite Housings Are Manufactured
The manufacturing process of GRP composite housings typically involves several steps:
1. Molding
GRP is often shaped using various molding techniques such as hand lay-up, spray-up, and compression molding. This flexibility allows manufacturers to produce complex designs efficiently.
2. Curing
The curing process solidifies the material, setting the resin and bonding the fiberglass to create the final product. This step is crucial for achieving the desired mechanical properties and durability.
3. Post-Processing
Once cured, GRP housings may undergo additional post-processing steps such as sanding, painting, or adding protective coatings to enhance performance and aesthetics.
The Future of GRP Composite Housings
As technology evolves, the future of GRP composite housings looks bright. Key trends include:
1. Sustainability Initiatives
With an increasing focus on sustainability, manufacturers are exploring eco-friendly resins and recycling practices to reduce environmental impacts. Innovations in biodegradable GRP composites could lead the way towards a greener future.
2. Smart Technologies Integration
The integration of smart technologies into GRP composite housings is an emerging trend. This includes sensors for monitoring conditions such as temperature and humidity, which are especially useful in critical applications like data centers and food storage.
3. Enhanced Manufacturing Techniques
Advancements in manufacturing, including automation and 3D printing, are expected to revolutionize how GRP components are produced, increasing efficiency and reducing waste.
4. Expansion into New Markets
As industries continue to discover the benefits of GRP composite housings, we can expect to see their adoption grow in sectors such as renewable energy, including wind and solar applications.
Conclusion
In summary, GRP composite housings offer a versatile, durable, and cost-effective solution for various industries. Their ability to resist corrosion, lightweight properties, and excellent insulation make them an ideal choice for applications ranging from electrical enclosures to marine environments. As we look to the future, innovations in sustainability and technology integration will further enhance the role of GRP composites in our daily lives. Businesses like Celtic Composites are at the forefront of this exciting field, paving the way for new advancements in composite materials.