The Essential Guide to Cylinder Engine Blocks: Innovating Diesel Power
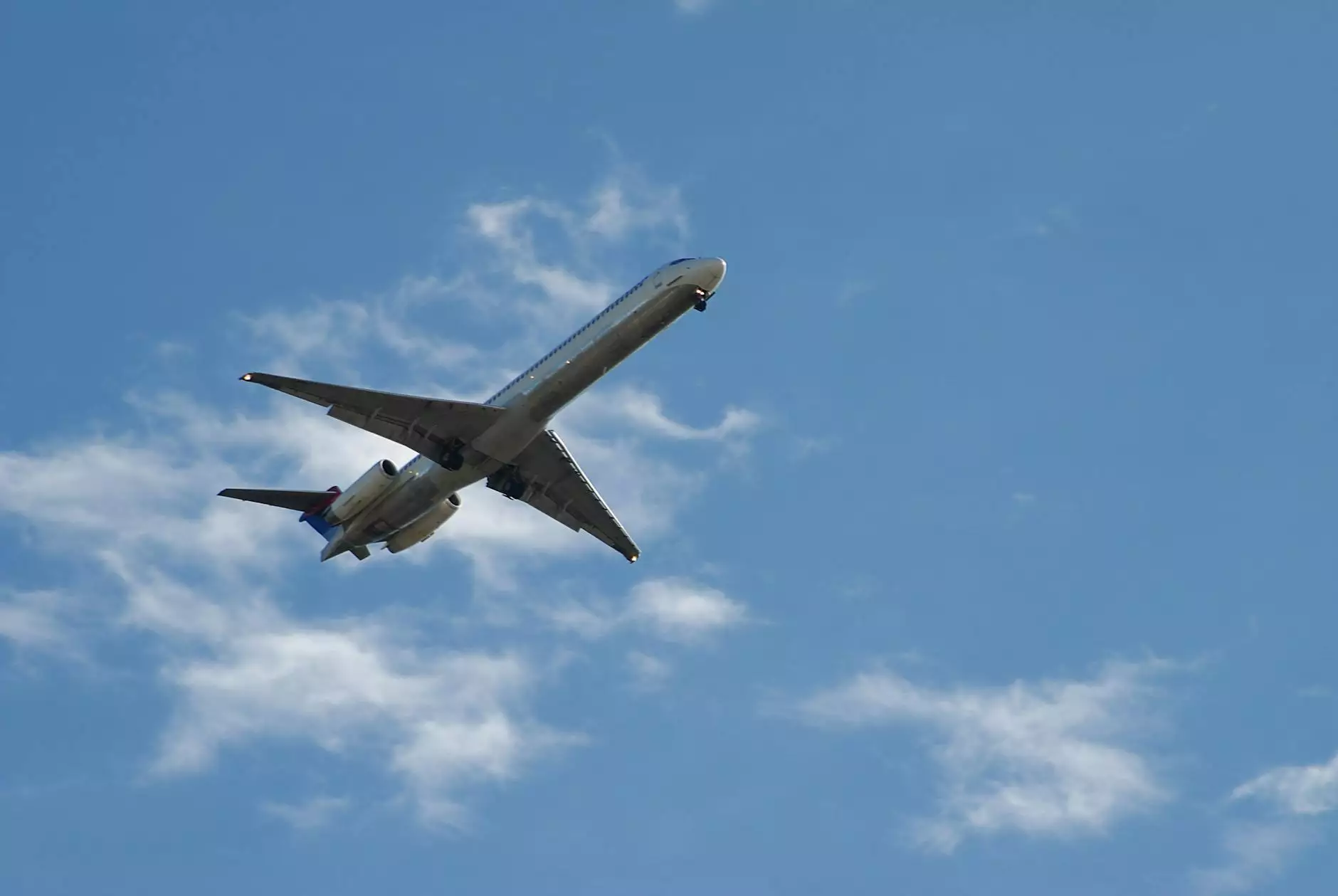
The cylinder engine block serves as the fundamental building block of any internal combustion engine. It houses various critical components, including the cylinders, pistons, and crankshaft, making it a crucial element in the workings of diesel engines. Understanding the intricacies of cylinder engine blocks not only helps in appreciating the engineering marvel behind modern automotive technology but also enables businesses, such as those in the diesel engine parts sector, like client-diesel.com, to provide superior products and services to their clients.
What is a Cylinder Engine Block?
The cylinder engine block is a vital part of a diesel engine, essentially acting as the engine’s core structure. It is typically made from cast iron or aluminum due to their excellent strength-to-weight ratios and thermal conductivity. The block contains multiple cylinders, which are the spaces where fuel combustion occurs, producing the power required to drive the engine.
Key Functions of the Cylinder Engine Block
- Holds Engine Components: The cylinder block supports the crankshaft, camshaft, and other essential parts, ensuring that the engine operates smoothly.
- Facilitates Combustion: It forms the walls of the cylinders that contain the combustion process, maximizing power output.
- Cools and Lubricates: Designed with various channels, the block helps circulate coolant and oil, maintaining optimal operating temperatures.
- Reduces Engine Noise: The mass of the block acts to dampen vibrations and absorb noise generated during the combustion cycle.
The Importance of Material Selection in Cylinder Engine Blocks
Choosing the right material for the cylinder engine block is crucial for engine performance and durability. Different materials offer various benefits and drawbacks:
1. Cast Iron
Cast iron is heavily used due to its excellent wear resistance and ability to absorb vibration. Its density provides strength and longevity, making it suitable for heavy-duty diesel applications.
2. Aluminum
Aluminum is becoming increasingly popular, particularly in newer lightweight diesel engines. It offers reduced weight, which can improve fuel efficiency; however, it may be less durable than cast iron under high-stress conditions.
Types of Cylinder Engine Blocks
Cylinder engine blocks can be categorized based on their configuration and cooling system. Understanding these configurations is essential for businesses that supply spare parts.
1. Inline Cylinder Blocks
Most common in diesel engines, inline cylinder blocks contain a series of cylinders arranged in a linear formation. This configuration is straightforward and effective for most automotive applications.
2. V-Shaped Cylinder Blocks
V-shaped or ‘V’ blocks contain two banks of cylinders in a ‘V’ arrangement, enhancing engine compactness and power output. They are often used in performance vehicles.
3. Boxer Engine Blocks
A boxer engine block features horizontally opposed cylinders, delivering a lower center of gravity, which improves vehicle stability. This design is less common but effective in specific applications.
The Manufacturing Process of Cylinder Engine Blocks
The fabrication of a cylinder engine block undergoes intricate processes to ensure precision and reliability. Here is a general overview of the steps involved:
1. Design and Modeling
Advanced computer-aided design (CAD) software is used to engineer the block, taking into account dimensions, material properties, and heat dissipation requirements.
2. Material Preparation
Raw materials, usually cast iron or aluminum, are prepared and melted down before being poured into molds to form the rough shape of the engine block.
3. Machining
After cooling, the block undergoes machining processes to achieve precise dimensions. This includes drilling holes for cylinders and machining surfaces for optimal sealing.
4. Surface Treatment
To enhance wear resistance and longevity, surface treatments may be applied, including coating processes that help in reducing friction and improving thermal management.
Performance Optimization Through Cylinder Engine Blocks
Performance optimization of diesel engines often hinges on the design and material of the cylinder engine block. Here are some ways in which businesses can influence engine performance by focusing on these components:
1. Heat Management
Effective heat dissipation mechanisms integrated into block designs can significantly affect engine performance. Businesses should prioritize blocks with superior heat transfer properties.
2. Boosting Compression Ratios
Reinforced blocks allow for higher compression ratios, which can lead to increased power output and efficiency. Customizing cylinder shapes within the block can optimize fuel combustion.
3. Lightweight Solutions
Implementing lightweight materials without compromising strength helps improve overall vehicle performance. For instance, advanced aluminum alloys can provide a viable alternative to traditional cast iron without added weight.
Challenges of Developing Cylinder Engine Blocks
The development of modern cylinder engine blocks does not come without challenges. Recognizing these challenges allows businesses to innovate and offer better solutions:
1. Achieving a Balance Between Weight and Strength
Manufacturers must continually refine materials to maintain a balance between lightness and durability, especially under high loads.
2. Managing Production Costs
While advanced technologies can enhance the performance of engine blocks, they often come with hefty production costs. Businesses must find ways to manage these expenses while delivering quality.
3. Adhering to Environmental Regulations
As regulations on emissions tighten, manufacturers are pushed to innovate greener production methods and design blocks that facilitate cleaner combustion.
Future Innovations in Cylinder Engine Blocks
As technology advances, the future of cylinder engine blocks looks promising. Emerging trends include:
1. Additive Manufacturing
3D printing technology is beginning to emerge in the automotive industry, allowing for the creation of intricate designs that were not possible with traditional manufacturing methods.
2. Advanced Materials
Research into composite materials that combine the best properties of metals and plastics could lead to further breakthroughs in weight reduction and strength enhancement.
3. Integration with Electrohydraulic Systems
Future cylinder blocks may incorporate integrated systems that further optimize engine performance through advanced control of fuel and emissions.
Conclusion: The Role of Cylinder Engine Blocks in the Diesel Engine Industry
In the realm of diesel engines, the cylinder engine block stands as an indispensable component, crucial for engine functionality, efficiency, and performance. For businesses like client-diesel.com, understanding the intricacies of these blocks translates into providing top-notch products and services that meet the evolving demands of the automotive market.
By prioritizing advancements in material science, manufacturing processes, and design innovations, businesses can ensure that they remain at the forefront of the industry, continuously enhancing engine performance, reliability, and sustainability. The future of diesel engines relies heavily on the evolution and optimization of the cylinder engine block, making this subject imperative for all stakeholders involved.